Condition Monitoring Platform
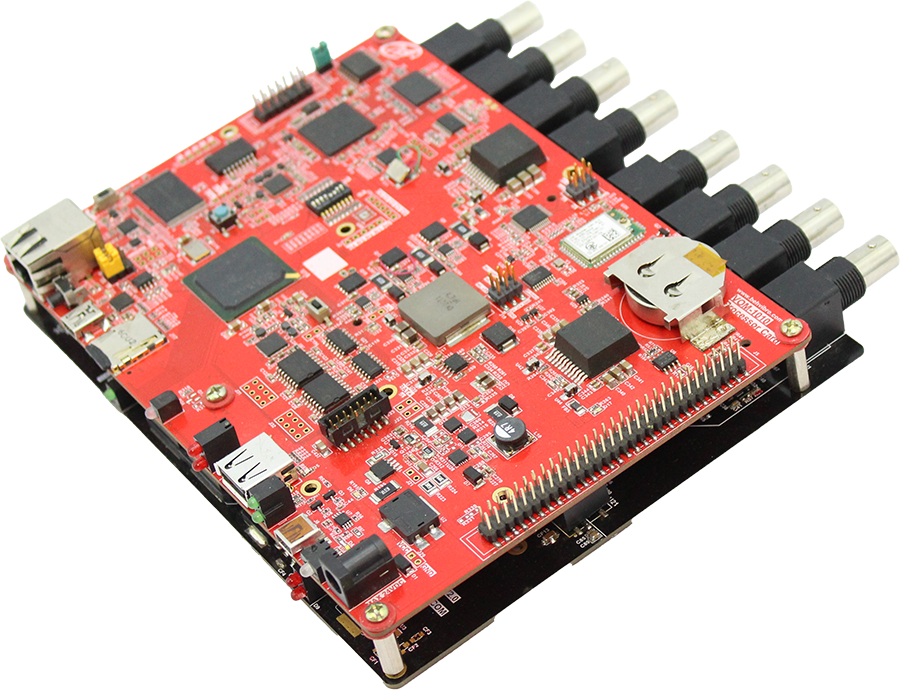
The VOM-1010 is a state-of-the-art condition monitoring platform designed specifically for harsh industrial environments, including those with large rotary machinery and electric motors. With extensive experience in embedded system design and mixed signal design, this platform is engineered to handle high-resolution, multi-channel simultaneous sampling inputs with exceptional sensitivity, capable of detecting signals as low as 10mV. Special attention has been given to ensure the reliability and accuracy of the VOM-1010, making it robust enough to operate in noisy environments typical of industrial settings.
Comprehensive Software Capabilities
The VOM-1010 is supported by a comprehensive software suite that offers advanced functionalities for data acquisition, processing, and visualization. The software allows users to set customizable parameters for data capture, ensuring that the system can be tailored to specific monitoring needs. It features synchronous recording capabilities that provide a complete view of machine health by capturing data from multiple sensors simultaneously.
One of the standout features of the software is its ability to perform real-time data visualization, along with historical trend monitoring. This functionality is essential for identifying patterns and predicting potential issues before they lead to critical failures. The software also includes configurable dashboards, enabling users to prioritize and monitor critical parameters efficiently.
Hardware Excellence
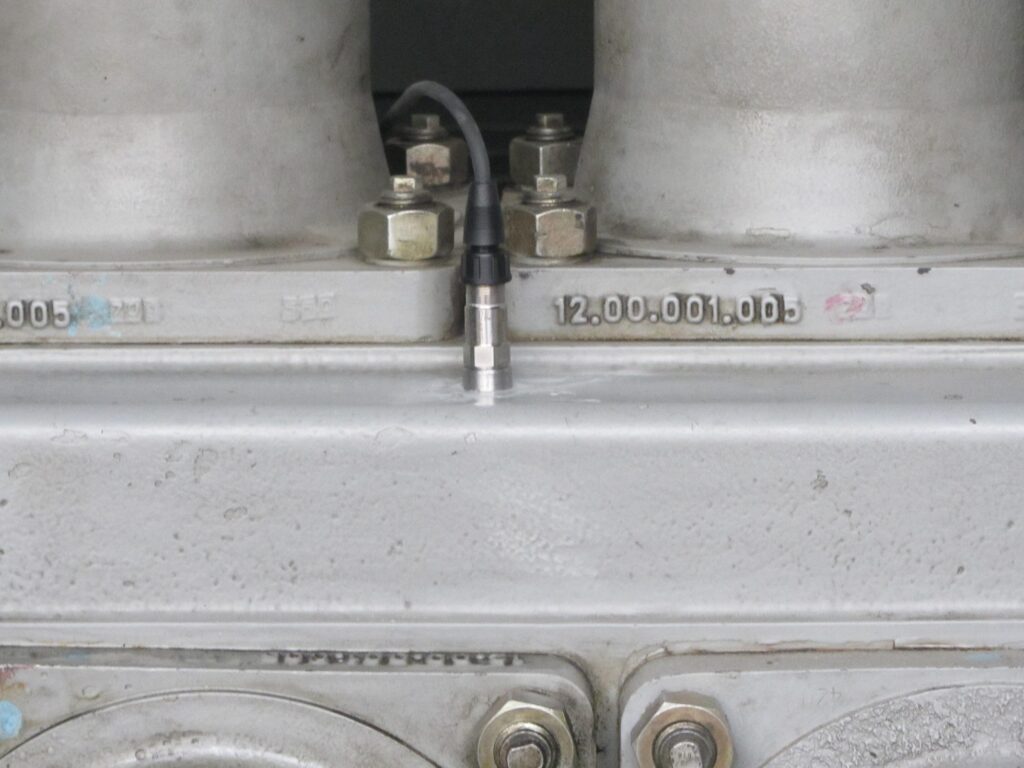
The VOM-1010 features up to 128 configurable input channels, allowing for extensive data acquisition from various sensors. The hardware is meticulously designed to ensure precise data collection and durability in challenging conditions. This multi-channel capability enables the system to perform synchronous sampling, which is crucial for accurate diagnostics and real-time monitoring.
The system’s design accommodates a variety of sensor types, including piezo accelerometers (Vibration), which the system can power directly, as well as tachometers, temperature sensors, and pressure sensors. This versatility allows for comprehensive monitoring of different machine parameters, ensuring a holistic approach to machine health management.
Technical Specifications
Processor Configuration:
- DSP + ARM Cortex-A architecture for advanced signal processing and control.
- FPGA integration for flexible, high-speed data handling and real-time processing.
Display Interface:
- Supports full-color LCD connection for on-site data visualization and user interaction.
Operating Systems:
- Dual OS setup featuring Linux for general applications and TI-RTOS for real-time, deterministic operations.
Input Channels:
- Supports up to 128 configurable input channels for a variety of sensors including vibration, temperature, speed, and more.
Sensor Compatibility:
- Compatible with piezo accelerometers, tachometers, temperature sensors, pressure sensors, and other industrial sensors.
Data Acquisition:
- High-resolution and sensitive data acquisition capable of detecting signals as low as 10mV.
- Designed to withstand harsh industrial environments, ensuring reliable performance amidst significant electrical noise and physical disturbances.
Power Supply for Sensors:
- Built-in capability to provide power to connected sensors, such as piezo accelerometers.
Data Processing and Analysis:
- Onboard capabilities for advanced signal processing, including filtering, FFT, and other algebraic calculations.
Storage Options:
- Onboard 64GB Flash memory.
- Expandable storage via SD-Card.
- SATA interface for additional storage options.
Connectivity:
- LAN for network communications.
- USB 2.0 ports for peripheral connections.
- Serial interface for legacy device support and additional connectivity options.
Environmental Robustness:
- Specially designed for deployment in challenging industrial settings, including environments with large rotary machinery and electric motors.